
Boosting Warehouse Efficiency with Cutting-Edge Material Handling Solutions
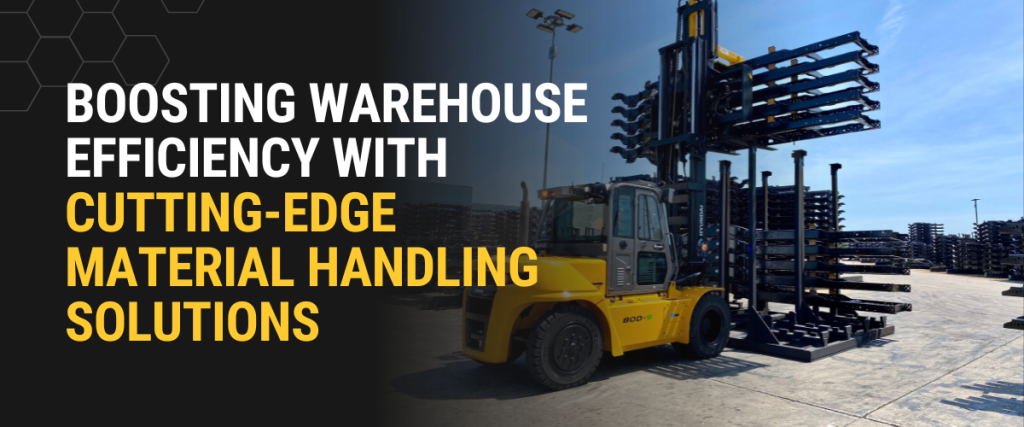
In today’s fast-paced business environment, warehouses and distribution centers are under immense pressure to optimize operations and improve efficiency. This is where efficient material handling plays a crucial role. By implementing the latest technologies and equipment, businesses can streamline their processes, reduce costs, and enhance customer satisfaction.
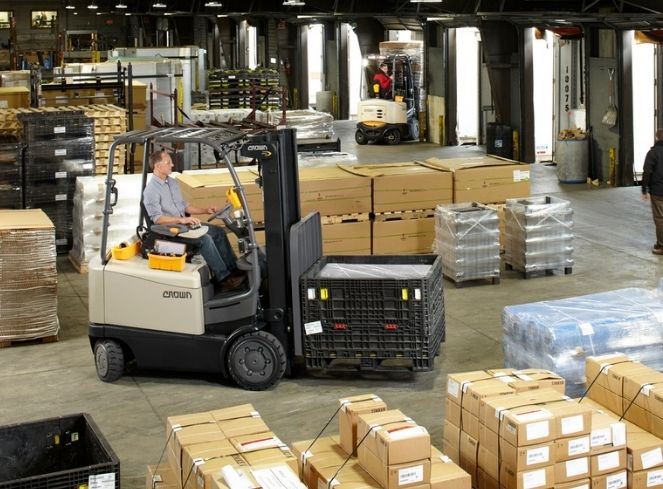
The Importance of Efficient Material Handling
In any warehouse or distribution center, efficient material handling is the foundation for maximizing productivity and reducing operational costs. The processes involved in moving, storing, and managing goods must be streamlined to ensure that the right products reach the right place at the right time.
When material handling systems are optimized, businesses can enjoy enhanced accuracy, improved safety, and significant cost savings, all of which contribute to a more efficient and profitable operation.
Efficient material handling is essential for:
- Increased productivity: Reducing the time and effort required to move materials can significantly boost warehouse throughput.
- Improved accuracy: Implementing accurate material handling systems can minimize errors and prevent stockouts or overstocking.
- Reduced costs: Optimizing material handling processes can lead to lower labor costs, fewer damaged goods, and reduced energy consumption.
- Enhanced safety: Advanced material handling equipment can improve workplace safety by reducing manual handling tasks and preventing accidents.
Cutting-Edge Material Handling Technologies
The rise of advanced technologies has transformed the material handling landscape, providing businesses with powerful tools to improve efficiency. From automation to intelligent software solutions, these innovations offer new ways to streamline operations, minimize errors, and reduce manual labor. Implementing cutting-edge material handling systems not only improves operational efficiency but also future-proofs the warehouse by enhancing scalability and adaptability to changing demands.
- Automated Guided Vehicles (AGVs): AGVs are self-guided vehicles that can transport materials throughout a warehouse without human intervention. They are equipped with sensors and software that allow them to navigate safely around obstacles and follow pre-programmed routes.
- Warehouse Management Systems (WMS): A WMS is a software system that manages all aspects of a warehouse operation, including inventory tracking, order fulfillment, and labor management. It can help optimize storage space, improve picking efficiency, and reduce errors.
- Conveyor Systems: Conveyor systems are used to transport materials between different areas of a warehouse. They can be configured in various layouts to suit specific needs, such as straight lines, curves, or inclines.
- Pallet Racking: Pallet racking systems are used to store pallets of goods in a vertical manner. They can be customized to accommodate different pallet sizes and weights, and they can be equipped with features such as barcoding and RFID for inventory management.
Tips for Selecting the Right Equipment
When choosing the ideal material handling equipment for your warehouse, it’s essential to consider several key factors. Thompson Lift Truck can provide expert guidance and tailored solutions to help you make the best decision.
1. Warehouse Layout:
- Aisle Width: Narrow aisle forklifts or reach trucks can be ideal for maximizing storage space in smaller warehouses.
- Ceiling Height: Consider the height of your warehouse to determine the appropriate lift capacity and mast height of your equipment.
- Traffic Patterns: Analyze the flow of traffic within your warehouse to ensure that equipment can move efficiently without bottlenecks.
2. Product Characteristics:
- Size and Weight: The dimensions and weight of your products will determine the necessary lift capacity and attachment types.
- Fragility: For delicate or fragile items, specialized equipment like order pickers or reach trucks may be required to handle them carefully.
Thompson Lift Truck offers a wide range of equipment options, including forklifts, reach trucks, order pickers, and specialized attachments to accommodate various product types.
3. Volume of Operations:
- Throughput: The volume of goods you handle will influence the required equipment capacity and automation level.
- Peak Periods: Consider your peak demand periods and whether you need additional equipment or automation to meet those needs.
4. Budget:
- Initial Investment: Evaluate your budget to determine the upfront cost of equipment purchase or rental.
- Ongoing Costs: Consider factors like maintenance, fuel, and operator training when calculating the total cost of ownership.
Thompson Lift Truck offers flexible rental and leasing options to accommodate different budgets and project requirements.
Key Takeaways for Optimizing Your Warehouse Operations
Efficient material handling is a critical component of successful warehouse operations. By investing in cutting-edge technologies and equipment, such as AGVs, WMS, and conveyor systems, businesses can significantly improve productivity, accuracy, and cost-effectiveness. By carefully considering your specific needs and following the tips outlined in this blog, you can select the right material handling solutions to optimize your warehouse operations and drive your business forward.
Key takeaways on boosting warehouse efficiency with material handling solutions:
- Efficient Material Handling: Enhances productivity, accuracy, cost savings, and safety in warehouse operations.
- Cutting-Edge Technologies: AGVs, WMS, conveyor systems, and pallet racking systems optimize movement and storage.
- Warehouse Layout: Equipment should be selected based on aisle width, ceiling height, and traffic patterns.
- Product Characteristics: Consider the size, weight, and fragility of goods when choosing equipment.
- Budget & Volume: Balance initial investment and ongoing costs with operational throughput and peak demand periods.