
Fluid Analysis
Avoid Unplanned Repairs or Catastrophic Failures
Thompson’s Fluid Analysis Service is one of the most useful and important maintenance support programs available. Using the Oil and Coolant Analysis, you can pinpoint trouble early and avoid shut-downs for unplanned repairs or catastrophic failures. It’s all about opportunity cost: if your machine is not running, you are not earning.
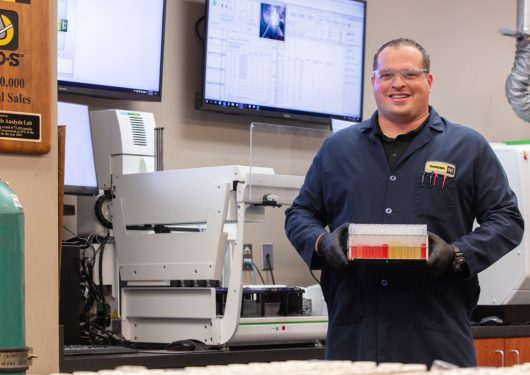
Early Detection through Fluid Analysis
Early detection delivers peak performance from your equipment. Fluid Analysis is a reliable, thorough, and cost-effective preventive maintenance program. It allows you to lower operating costs and to schedule downtime for necessary repairs.
Thompson Lift Tractor’s fluid analysis lab in Birmingham operates with one primary goal in mind – Enabling our customers to get the most out of their equipment.
Our experience tell us that preventive maintenance and cost-effective before-failure repairs are two important tools that regular oil sampling can provide. Test results are analyzed against previous results to monitor for abnormal wear trends. We give the customer an overall evaluation and recommendation. An oil analysis form is then printed and mailed, faxed, or emailed to the customer.
The best oil sample data comes from proper sampling techniques. Consistent hours or mileage on each oil sample submitted, along with the weight of the oil being used enables the best interpretation. Thompson Lift Tractor’s lab provides complete lab services – such as particle count testing, oil condition analysis, wear metals analysis, viscosity testing and coolant analysis – to monitor your equipment. This enables you the efficiency of scheduling maintenance and forecasting repairs that optimizes your equipment’s productivity.
- Particle Count Testing
Particle count testing detects larger particles in the oil than the ones found in typical wear metal analysis. This provides our customers with another tool for the detection of excessive wear and contamination. - Oil Condition Analysis
Oil condition analysis compares a customer’s current used engine oil sample with a previously recorded sample of their new unused engine oil to detect the amount of lubrication the oil may lose during normal operation. This potential loss of lubrication can be from several sources such as soot, oxidation, and sulfur. Engine oil contamination from fuel, water and coolant entry can also affect the oil’s ability to lubricate more. All of these various contaminants are recorded and reported. - Wear Metals Analysis
Wear metal analysis measures and identifies the amounts and types of metals that wear inside an engine, transmission, final drive, or hydraulic system. Nine different metals are recorded and evaluated in order to monitor the wear inside each of these compartments. The wear metal readings are measured and recorded in parts per million, which is the industry-wide standard for reporting metal analysis results.
Dependent upon the level of metals in the oil, we will determine where the abnormal wear is originating within a compartment.
We test for Aluminum, Chrome, Iron, Lead, Potassium, Silicon, Sodium, and Tin.
Coolant Analysis
Coolant or cooling system problems contribute to more than 50% of all engine failures. These failures can be due to inadequate cooling system maintenance, incorrect coolant concentrations, and poor operational procedures, all of which can cause accelerated oil degradation, insufficient heat transfer, corrosion of liners, water pumps, and seals. Coolant analysis can determine the overall condition of the cooling system and can identify problems with maintenance procedures and practices. Level 1 coolant analysis consists of four analytical tests and three observational tests that not only show major problems with the coolant, but can also predict some major coolant system problems. Cooling system problems will also reduce the life of engine, transmission, and hydraulic components served by coolant heat exchangers. Coolant analysis is as important a tool in early prediction of potential problems, as oil analysis is in oil-lubricated systems.
Do you have any questions? Fill out the form below or contact:
Tony Harris, Supervisor / (205) 244-7865 / [email protected]